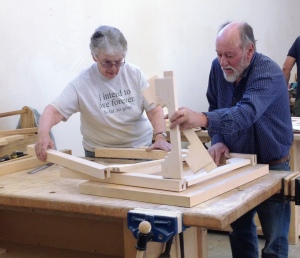
Professor James Rannefeld helps a student prepare for gluing up the base of her Spanish Colonial end table project in the wood shop at UNM Taos.
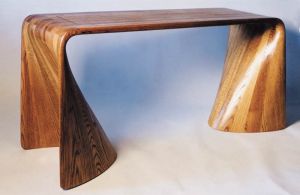
Inspiration bench, in oak. Rannefeld wrote about the laminated joinery technique used to build it for Fine Woodworking magazine in 1983.
James Rannefeld was a restless young man with two science degrees when Taos’ sluggish, mid-70s construction industry forced him to abandon his carpentry career for something more stable.
Determined not to fall back on geology or oceanography, he instead became a woodworker.
Surrounded by fine artists who were selling and shipping their work to collectors around the country, Rannefeld started making his living, in part, by building the crates. A few years later, he was showing his own sculptural woodwork through galleries in Taos and Santa Fe, building custom hardwood doors for designers in Dallas and fine furniture for sale in boutiques on both sides of the Atlantic.
He wrote for Fine Woodworking magazine, and he became an employer, keeping 10 workers busy building his Southwest style designs in a shop near Taos’ plaza. Unscrupulous competitors and changing public tastes eventually sunk that enterprise, but Rannefeld never quit designing and building one-of-a-kind work.
Like many woodworkers, he also became a
teacher. At the University of New Mexico’s branch campus in Taos, he is an associate professor and director of the school’s fine woodworking program, which he founded in the early ’90s. After four decades in woodworking, he still has plenty of lessons to share.
What he doesn’t have is enough students.
The program, which offers a Certificate in Fine Woodworking, has been enrolling 60 to 70 students per semester. Rannefeld said he’d like to see those numbers climb to at least 90 to 100 to help insulate the program from any future cutbacks.
Students seeking certification start with 18 semester hours of woodworking and furniture-making fundamentals. The program’s mission, Rannefeld says, is to “give them the basics. Give them the foundation, and let them build on that.”
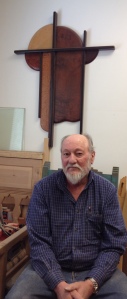
Rannefeld in his office, with his Quattro wall-hung sculpture. The piece is assembled from shaped, solid hardwood.
The core courses are followed by 12 hours of electives, which can include sculpture, lamination, bending, and carving among other techniques. The program also offers an introductory business course and a semester of instruction on Quickbooks accounting.
Some students are intent on pursuing the craft for its own sake; others are fine artists learning to work with wood as an expressive medium. Almost all, he says, recognize the need to preserve the elements of the craft.
On a recent afternoon, the shop was alive with the sound of grinders and dust collectors as some students shaped and smoothed sculptural work while others cut joinery or prepared for assembly. Rannefeld circulated around the shop, stopping at each bench, offering pointers and asking questions.
Later, he shared with me a piece of advice he gives often – a lesson learned early: “Make it better than it has to be. That way you can sleep at night.”
Enrollment for the fall semester at UNM Taos is underway now. Visit http://taos.unm.edu/academics/fine-woodworking.html for more information on the woodworking curriculum.